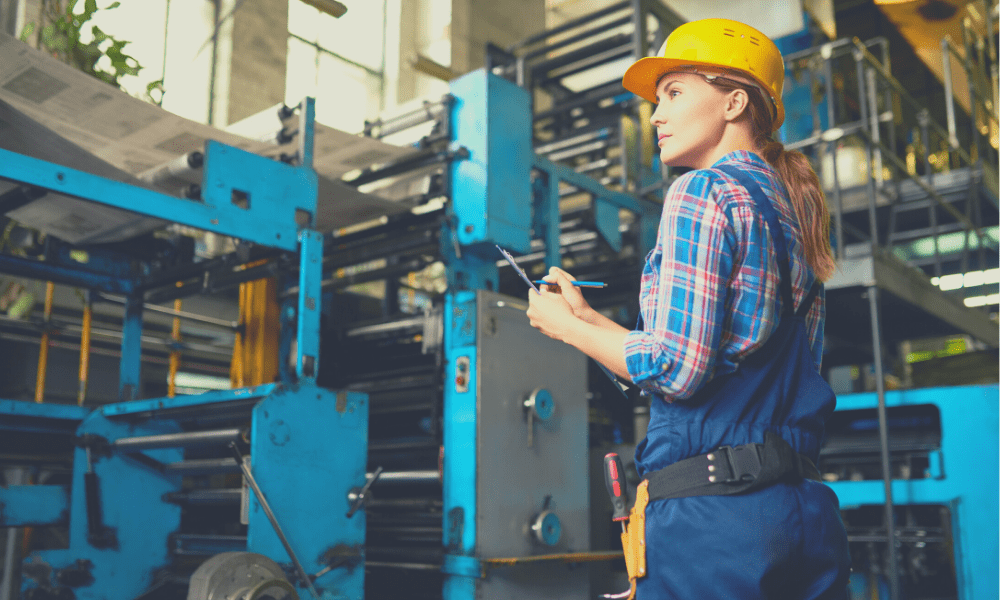
If there’s ever been a year that merited reflection, it’s 2020.
A year as tumultuous as the last is hard to generalize – what did we actually learn about manufacturing?
The answer is best given by the people who lived these changes. As a disclaimer, there was simply too much to cover in one article. (Supply chains, for example, deserve their own treatment).
Here are the biggest lessons we learned about manufacturing in 2020:
People are necessary
There are two competing narratives about human work in manufacturing during and after COVID-19.
On the one hand, there’s a real anxiety that firms are going to fast-track their automation programs, leaving workers out of the job. On the other, there’s the story that I heard from a number of manufacturers: No people, no production.
“We learned not to underestimate our people,” said Jennifer Davis of Arch Systems. “We just witnessed the most unlikely employees effectively adopting technological tools. Most of all, we learned to see people as people – at every level of our companies.”
I heard a version of this refrain – of workers learning and adapting and persevering – over and over.
Indeed, what we really learned is that the dichotomy of automation vs. workers is painfully blunt and woefully misleading.
There’s a much more nuanced conversation to have about the nature of work, skilling and reskilling, and some of the world’s leading organizations are creating channels for having those talks. Manufacturing workers are becoming knowledge workers.
As Simon Jacobson, VP Analyst at Gartner excellently summarized, “Labor is the new constraint and needs attention. Manufacturers that continue to rely on tacit know-how and do not invest in knowledge management and transference will struggle with capacity utilization.”
In short, we learned that manufacturing will only be as successful as it’s people.
Collaboration can make big things happen
Collaboration and partnership can be good strategy. So the massive collaborations we saw this year were a difference in degree, not kind. And it was a huge difference.
Girish Wabel, a Senior Manager of Strategic Capabilities at Jabil, captured the distinctive nature of these collaborations when he noted, “You saw manufacturing giants take on projects completely out of business plans but not unlike their character, for example PPE and ventilators. It showed the power of great collaboration and what can be achieved or the devastation it can cause when people don’t selflessly collaborate.”
There are so many examples of collaboration from this year, but one stands out.
Two of the companies I’m affiliated with– Tulip and Formlabs – had the privilege of working with the non-profit MasksOn.org. MasksOn is a model of what selfless, innovative collaboration can do. Uniting leaders in industry, academia and healthcare, MasksOn provides frontline healthcare workers with protective head masks made by fitting a viral filter on an off-the-shelf snorkel mask with a 3D printed adapter. The organization handles everything from order processing, to manufacturing, to fulfillment. To date, they’ve shipped 30,000 pieces of cutting-edge PPE across the world.
If the next year’s challenges are anywhere near as trying as this year’s, we’d do well to remember what can happen when we work together.
Distributed manufacturing builds resilience
This trend is probably best understood as an extension of collaboration, but it deserves its own point.
To date, manufacturing has been site specific. It’s done at the plant, or as part of a carefully planned and integrated supply chain.
This year showed us there are other ways.
When shutdowns and supply chain interruptions halted production, manufacturers looked for capacity anywhere they could find it. What emerged were distributed manufacturing networks, where individuals in spatially distant geographic areas worked collaboratively on the same projects.
For one, additive manufacturing organizations asked their customers to volunteer their machines to print nasal swabs and PPE. Others offered their intellectual property – in the form of CAD files, BOMS, work instructions and supplier lists – to manufacturers with capacity to produce ventilators.
I’ve long argued that manufacturing needs to model open source, as much in spirit as in practice. These distributed manufacturing networks are one step closer to that ideal.
Agility is key to survival
If nothing else, 2020 was a great year for buzzwords.
“Unprecedented,” “new normal,” “difficult times.”
Which is why I worry that one of the main lessons of 2020, the need for agility, runs the risk of winding up buried beneath a pile of meaningless buzzwords.
Organizations learned that rigidity is risk, and that being able to adapt to unforeseen circumstances is a competitive advantage.
We learned that change is the status quo. We are not just weathering a storm, gritting our teeth until the “new normal” arrives. Rather, we accept change as a constant and build adaptability into our organizations and operations.
Change is only accelerating
As Microsoft CEO Satya Nadella put it, the world experienced two years of digital transformation in two months.
This pace is set to continue. In a recent survey, 58% of operations leaders reported that accelerating digital transformation was a top priority.
But this acceleration brings new challenges, and it isn’t just about tech. Navigating the dynamic landscape requires equal attention to the cultural and technological dimensions of transformation.
Manufacturing can support remote work
Remote work has been one of the big stories of the pandemic.
And if you asked the industry a year ago, I’m positive only a few would have believed that manufacturing could support remote work.
Nevertheless, manufacturing has adapted to a remote world.
Dave Margetts of FactoryTalk expressed a characteristic thrill at the prospect of an increase in remote work. “We’ve learned we can deliver even complex projects entirely remotely. Gone are the days of endless flying around the world supporting manufacturing IT implementations!”
Audra Kirkland of Terex found that moving to remote provided an opportunity to update their training processes. “We normally have peer training,” Kirkland started. “We’re moving through a guided work approach where we’re having people learn on the job as they’re doing the work, but through a guided process without a human having to be right next to them. It’s been eye-opening how we can use technology in order to limit exposure in the future now that we know what the future may hold.”
For 2021? Focus on work
While it’s important to keep thinking about the future of work, 2020 showed us that we need to look closely at how manufacturers are working now.
2020 augured fundamental changes in how manufacturers work, where they work and working methodologies. And these changes aren’t going to slow any time soon.
So here’s to taking what we learned last year and keeping the conversation going into years to come.